No ballistic barrier is complete without ballistic panels (often referred to casually as "bulletproof drywall"). That's because, although cinder block and brick will stop most common bullet calibers, standard construction drywall will not. In fact, a 9mm bullet will penetrate more than two dozen sheets of half-inch drywall and still be able to do harm. That bullet will likewise pop through several layers of plywood—and even through stacks of two-by-fours.
In other words, most places people take cover—down beneath a counter or desk or in a locked room—really don't offer much better protection than a row of hedges. But adding even a single .25 inch ballistic panel to that wall or reception desk will stop those 9mm bullets cold.
That said, Total Security Solutions CEO Jim Richards has found that “ballistic panels are often neglected by companies who don’t take a 'system' approach to bullet-resistant security.” This is a natural consequence of how most people enter the ballistic security field. If you start out as a glazier and branch into offering security glazing, you will tend to focus on windows. "Customers are the same way," Jim points out. "Windows are where everyone focuses, and then doors. The bulletproof panels are literally invisible, and that makes them easy to forget."
Although it's often easier to install ballistic panels during construction, they are regularly retrofitted to existing locations.
An Introduction to Ballistic Panels
“Bulletproof drywall” isn't drywall. It's UL-rated bullet-resistant fiberglass that goes under drywall, wood paneling, or veneer. Ballistic panels come in rigid sheets (like plywood or drywall—hence the name). Depending on the security level, your ballistic panel can range from .25 to 1.5 inches (for comparison, most drywall is .5 inches).
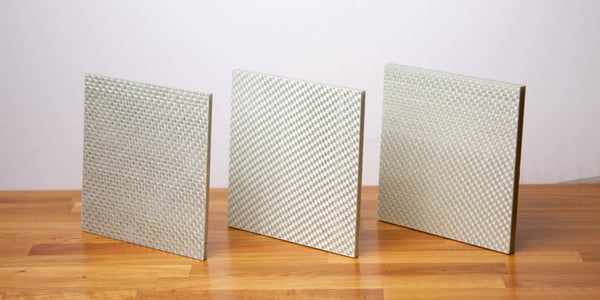
As with many ballistic materials and barriers, it's best to think of ballistic panels as being in one of two categories: Level 1–3 or Level 4+.
Level 1–3 materials are engineered to stop clusters of shots from a variety of handguns. Ballistic panels in this category are between .25 and .5 inches thick. Although the material is much harder than drywall or plywood, it can usually be cut and drilled on-site using conventional tools (provided you use carbide or ceramic saw blades and drill bits). Even contractors who have never worked with ballistic materials or fiberglass before can usually install Level 1–3 panels without too much trouble.
Level 4+ materials are engineered to stop many shots from various long guns (including high-powered and tactical "assault" rifles, shotguns, and so on). These are weapons and bullets designed for maximum penetration and are thus significantly harder to stop than pistol rounds. As a result, Level 4 ballistic panels are generally at least three times thicker (and thus three times more expensive) than Level 1–3 panels.
For example, a Level 3 panel is .5 inches thick. A Level 4 panel is roughly 1.5 inches thick (i.e., about as thick as two packs of playing cards). While Level 4+ materials can, in theory, be cut and drilled on site, it is going to be slow work and will be hard on tools. Anything beyond minimal trimming or drilling a few holes will likely not be practical, even for experienced contractors.
Ballistic Panel Installation: Renovation/Retrofit
You can approach a ballistic renovation in several ways. Some facility owners—especially if they are going with Level 4 security or higher—choose to tear out all of the old drywall, secure the new ballistic panels directly to the studs, and then layer new drywall over the top. It's extremely hard to drill or drive a nail into bullet-resistant fiberglass, so having that outer layer of drywall will make it easier for future contractors or building occupants to hang pictures and sconces, mount switch plates, attach new trim and molding, and so on.
In other situations—especially where you're using Level 1–3 materials—you might simply choose to mount the ballistic panels directly over the existing drywall. You can then add another outer layer of drywall or simply prime and paint the fiberglass itself (despite the cross-hatched appearance, the surface is actually finished smooth on most ballistic panels).
You can likewise enhance the security of existing counters, reception desks, and half-walls. In most cases, contractors will mount precut ballistic panels to the interior of a reception desk or counter. Alternatively, the ballistic panel can be secured to the outside of the built-in furniture and then painted or veneered to blend with the building's interior.
Ballistic Panel Installation: New Construction
New construction is more straightforward: Simply mount the ballistic panels to the studs and then cover with drywall. Roughly half of all the ballistic paneling TSS sells goes directly to contractors for jobs like these.
“The fiberglass itself, in the scheme of things with ballistic materials, is inexpensive,” Jim explains. "So sometimes what we see in new construction is that they decide to install the bulletproof drywall now, knowing that they may ultimately determine they need a full ballistic security barrier at some point in the future. Later, converting that room to a 'safe room' is as simple as hanging a new UL-rated door. That's hardly any labor at all. Even replacing windows or adding backglazing is pretty straightforward, compared with going back in and redoing all the walls."
Maximize Protection and Value with Complete Professional Ballistic Barrier System Installation
"Regardless of security level," Jim explains, “Having a full system fabricated, rather than buying it in pieces and having a local contractor handle it, is usually best."
This is because, especially with ballistic fiberglass panels, you can see significant savings by having a system fabricated instead of simply buying a stack of sheets of paneling to cut and install on your own.
"We cut it on a CNC water jet, not by hand. The layout and holes are uniform, with good square cuts and tight corners. All the cutouts for power boxes and receptacles, doing that with a drill and jigsaw is very slow going in the field. So, when we cut the pieces, it isn't just that you save time not having to make those cuts. It also means the installation is easier, and the fit and finish end up nicer. But you are also saving money because we can be so much more efficient with materials. We can yield it and nest your job in with other jobs we're fabricating. You don't end up buying a full sheet because you need one more twelve-inch strip to finish a wall. With a fully fabricated system, the buyer just pays for what they need for their job."
Thinking about securing your building? Give TSS a call today to discuss what options are best for you.