Total Security Solutions works hard to absolutely minimize business disruptions for their clients. In most cases, TSS ships a ready-to-install bullet-resistant barrier system four to six weeks from the time the customer greenlights the project. In almost every case, if TSS is handling the installation, they will have that system fully installed overnight or in a single weekend.
Faster Delivery of Better Barrier Systems
These timelines may seem hard to believe—especially if you have any experience with commercial contractors. And you’re right to be incredulous. At one time, the idea of designing, fabricating, finishing, shipping, and installing a custom ballistic barrier in just a month would have seemed laughable. Until about ten years ago, fabricating the bulletproof glazing, fiberglass, and steel required for such a barrier system was largely done by hand in smaller shops, relying on labor-intensive, multi-step processes.
Raw materials—be they steel, fiberglass, monolithic acrylic, or glass-clad polycarbonate—would arrive in large sheets. Workers would cut these into “blanks”—the basic door or window shape—using a granite saw. They then hauled the blanks to a separate shop to be routed, drilled, and milled by hand. This was time-consuming. And much of that time wasted moving materials from station to station or finding places to store items between operations.
TSS was early to adopt modern automation, like computer-controlled (CNC) water jet cutters, and to seek out workers with the skills to make the most of it. Over the last decade, this has proven a massive time-saver. It’s also allowed TSS to steadily improve the quality and aesthetics of their barrier solutions.
Time savings alone could justify the investment in automation. A water jet cutter reduces all of that cutting, carting, routing, and drilling to a single step. It can slice a four-foot by eight-foot sheet of fiberglass into 10 or more pieces in less than 15 minutes. That includes all cutouts, notches, and mounting holes. From there, the pieces can go straight to finishing or installation, with no further hand fabrication. That’s half the time such a job once took.
Shorter Timelines, More Complex Fabrications—All Thanks to Automation
Water jet cutters spray a narrow stream of abrasive particles—like garnet—at ultra-high pressure between 30,000 and 90,000 psi. This is how they cut, by reproducing the irresistible natural process of erosion. As such, they can cut through any thickness of most materials. A water jet cutter can fabricate entire stacks of steel, fiberglass, or bulletproof glazing at once.
This has also unlocked a whole new set of materials and design approaches. A CNC water jet cutter can execute long smooth curves and other cuts that would have previously been prohibitively expensive, or even impossible, using older tools. For example, with a water jet cutter, TSS can add speak holes and other detailed cuts to glass-clad polycarbonate. This makes it possible to create functional barriers—like teller windows—that look like traditional bullet-resistant barriers but can stop many more bullets of much higher calibers.
“When it comes to commercial bulletproofing for buildings, we’ve driven a lot of tech into this industry,” explains TSS CEO Jim Richards. “We try to drive more in, but this is still a pretty old-line industry. You’d be amazed how much is still done by hand in many shops.”
Hand building is both slower and less precise. As a barrier system gets larger or more complex, it becomes more and more likely that tiny imprecisions will stack up into big problems. In such cases, the only solution is re-engineering or new pieces. Late starts and ballooning installation times inevitably follow.
Sticking to Schedule Despite COVID Supply Chain Challenges
Longtime TSS clients might be surprised to see that these four-to-six-week standard timelines have remained largely the same—despite the supply chain shocks associated with the nearly two-year-long COVID pandemic. You have to wait 12 weeks to get a bike or dog bed ordered online, but TSS can keep the same schedules they did in 2017?
Of course, TSS has not been immune to the global pandemic. TSS is experiencing the same shipping delays as everyone else, with lead times for some materials from 12 weeks to 27 weeks. Costs for supplies jumped, too. By last spring, acrylic prices had jumped twice, steel prices increased by 20%, aluminum prices by 30%, and shipping materials more than doubled.
Obviously, doubling prices and lead times were entirely unacceptable. Instead, TSS invested in expanding our network of suppliers, locking in secondary and tertiary sources for materials, pre-buying supplies, and holding as much inventory as possible.
“All of our standard materials—acrylic, LP 1250, bullet-resistant framing—we stock and keep in-house,” Jim says. “That has done a lot to insulate our customers from the supply chain chaos and keep our timelines in order. But things we have to get from someone else are outside of our control. We’re at the mercy of the manufacturers, just like everyone else this year.”
Bullet-Resistant Barrier Timelines for a “Small Project”
For most “small” bulletproof projects—like a utility or city office, mobile phone shop, or other retailers—TSS can have their bullet-resistant barrier in place in about a month.
For example, consider a small retail project like this one:
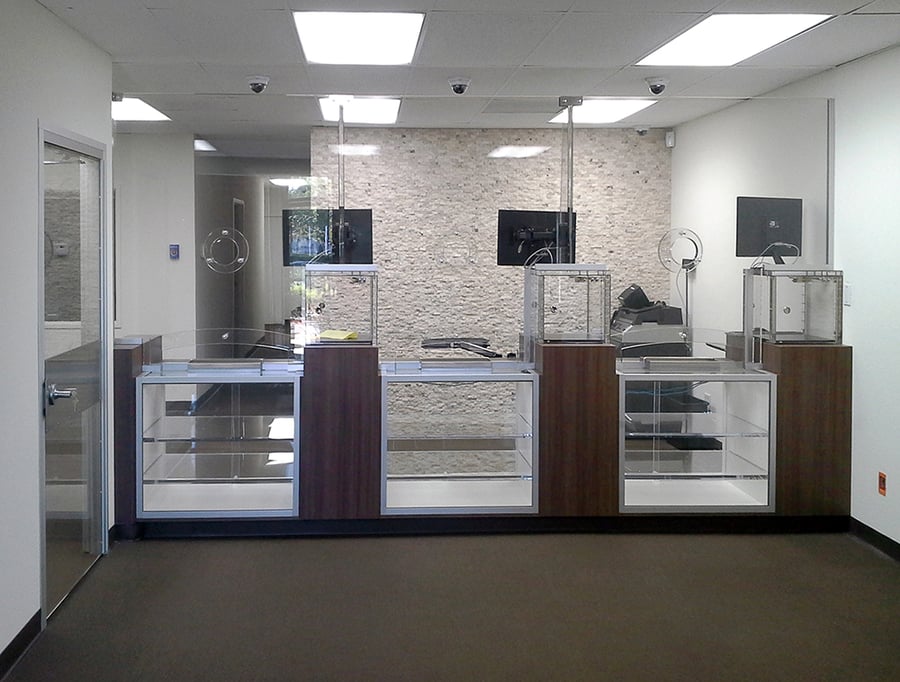
A “small” bullet-resistant barrier solution with extremely high-visibility
Such jobs often have three point-of-sale or reception stations, with one or more passers for exchanging documents, accepting deliveries, or dispensing goods. The “bulletproof glass” in the windows would probably be something like LP 1250 glass, a laminated material that combines layers of thermoplastic and tempered glass. The result is a clean, durable, optically sharp material able to provide “Level 3” security (that is, capable of stopping multiple shots and clusters of bullets fired from any common pistol). The framing would be similarly security rated and any wooden counters would be backed with ballistic fiberglass.
In most cases, following an initial call and collecting dimensions, it takes TSS less than one week to produce approval drawings for such a project. Once the customer returns the signed drawings, furnishes all info (confirming materials or hardware options, etc.), and pays a deposit TSS gets to work. They can have that project engineered and in production within a week. In most cases, it will ship (ready to install) three weeks later.
Bullet-Resistant Barrier Timelines for a “Larger Project”
A bigger, more complex job typically takes around six weeks to ship once drawings are approved. Such a job might include an entire storefront: exterior windows, two or three sets of double doors, and more heavy-duty materials like glass-clad polycarbonate (or “GCP,” which has four- to six-week lead-time on its own, because of the way this especially strong and durable glass is manufactured).
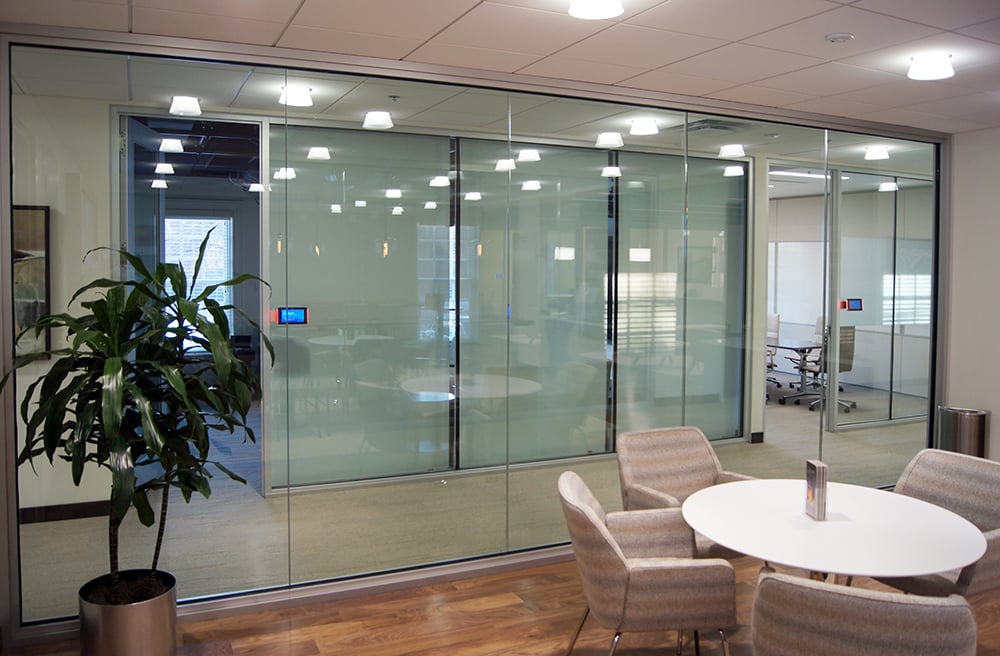
even “large” bullet-resistant barrier solutions can seamlessly blend into the building aesthetic
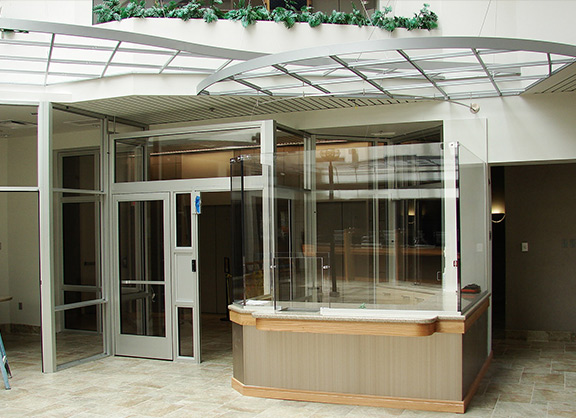
large bullet-resistant barrier solutions include more custom elements
“But keep in mind,” Jim Richards is quick to note, “there are all sorts of different variables at play. For example, if a customer has a door and picks some kind of very specific door hardware that’s in short supply, there could be six weeks of lead time on that door hardware. The whole rest of the system might be ready to ship while we wait weeks for door hardware to show up so we can mount the bullet-resistant door in the appropriate frame.”
What’s the Minimum Time to Deliver a Custom Bullet-Resistant Barrier?
Four and six weeks are typical project timelines. Hearing that leads many to ask “Well, then, what’s the fastest we can get this done?”
That’s extremely hard to say. TSS may be able to design, engineer, and fabricate the entire system. But it makes no sense to install it if the doorknobs you wanted won’t arrive for another two months. But, provided a customer has the resources to put into a project, even a very large project can be completed amazingly quickly.
Working Fast and Flexible to Craft a Custom Bulletproof Barrier
In the spring of 2018, Total Security Solutions was contacted about a novel custom bulletproof barrier project. The client was a very high-profile foreign dignitary. The dignitary would be working and staying in a variety of locations across the United States—some of which badly needed a security upgrade.
Two of these locations were in hotels, one on each coast. Once TSS designed, engineered, and fabricated the bulletproof barrier system, local contractors could handle installation (with TSS support). But the third location was an extremely large luxury home and the property owners had no interest in permanently fortifying their mansion. Subsequently, TSS installers would travel to the site and secure the home with seamless temporary barriers.
The job called for roughly 4,500 square feet of custom ballistic glass capable of stopping 5.56 NATO-issue rounds. (These are the bullets AR-15 style tactical and assault rifles fire.)
At that time and in the normal course of business, delivering a job this size would take eight weeks. The industry standard for production time alone would have been four weeks.
“We have an amazing crew [at Total Security Solutions],” explained Tim Bean, who was TSS Operations Manager at that time, “These guys will do whatever it takes to get this done. But it’s more than manufacturing. It’s logistics and trucking, too. It takes coordination from several different parties to actually make it come together.”
And these customers didn’t need their project delivered in the industry-minimum of four weeks. They needed it in five days. And two days in, the dignitary’s security detail called with further requests, in essence doubling the job.
Working with a Client to Rise to the Challenge
“You’re dealing with a customer,” Tim explained, “and a kind of person that when you say ‘That’s not possible,’ that doesn’t exist in their realm of thinking about the world. To them, it’s not that it’s not possible, it’s just that I’ll give you more money, and you’ll make it happen.”
For example, the level of security the dignitary’s team specified would normally require Level 8 transparency. Level 8 bullet-resistant glass is made by laminating many layers of tempered glass and blast-rated polycarbonate with intervening layers of epoxy. It cannot be fabricated with conventional tools and is generally only manufactured on an as-needed basis.
“I don’t care who you call,” Tim said, “you can’t get Level 8 windows in 24 hours. You can’t get them in a week. They’re made in an autoclave; they’re specially glazed. If anyone else tells you that they can get you Level 8 glass to your size in a couple of days, they’re lying. It can’t be done.”
But this dignitary came from a place where no one ever answers, ‘this just can’t be done’. So TSS flexed their engineering muscle. They designed a custom system of double-layered Level 3 acrylic mounted in their proprietary framing. They mocked up a prototype and the dignitary’s security team personally tested them to their specifications. The result was that the custom back-glazing stopped NATO 5.56 and Winchester .308 rounds—some of the hardest calibers to block.
Exceeding Expectations with Custom Bulletproof Barriers
“What would normally take us three to four weeks in production time, we got it out in 36 hours,” Tim noted. “And we built to a security level that, at first glance, you’d say couldn’t be done, not on that timeline. . . . I think that’s what makes TSS so unique. We have the ability to act that fast because of the crew we have, our shop is very streamlined, we know what we’re doing, and we stock the product to be able to fulfill those orders. Jim [Richards, TSS’s CEO] is very good at forecasting, which means we have a lot of material on hand and carry the inventory needed for seemingly one-in-a-million situations like this.”